Fixed gas detectors are critical tools in the realm of safety and risk management, designed to continuously monitor the presence of hazardous gases in specific locations. Unlike their portable counterparts, which are carried by individuals for temporary or spot checks, fixed gas detectors are permanently installed in areas where gas leaks could pose significant threats to human health, property, or the environment. These devices play an indispensable role in industries, commercial spaces, and even residential settings, providing early warnings and enabling rapid responses to prevent disasters such as explosions, toxic exposures, or fires. This article delves into the nature of fixed gas detectors, exploring their functionality, types, applications, benefits, and challenges to highlight their importance in maintaining safety across diverse contexts.
Understanding Fixed Gas Detectors
At their core, fixed gas detectors are stationary instruments engineered to detect and measure the concentration of specific gases in the air. They are typically integrated into a facility’s safety infrastructure, often connected to alarms, control systems, or ventilation units to trigger immediate action when gas levels exceed safe thresholds. These detectors are designed to monitor a variety of gases, including flammable ones like methane and propane, toxic gases such as carbon monoxide and hydrogen sulfide, and oxygen depletion, which can signal an unsafe atmosphere.
The operation of fixed gas detectors relies on sophisticated sensor technologies tailored to the target gas. For instance, catalytic bead sensors detect combustible gases by measuring heat from oxidation, electrochemical sensors identify toxic gases through chemical reactions, and infrared sensors analyze gas absorption of light wavelengths. When a gas concentration surpasses a pre-set limit, the detector activates an alert—be it an audible siren, flashing light, or digital signal—allowing personnel to evacuate, ventilate, or shut down operations as needed.
Types of Fixed Gas Detectors
Fixed gas detectors come in several configurations, each suited to specific monitoring needs and environmental conditions. The main types include:
- Point Detectors: These are the most common fixed detectors, designed to monitor gas levels at a single, specific location. Installed near potential leak sources like valves, pumps, or storage tanks, they provide precise, localized detection and are ideal for confined spaces or equipment-heavy areas.
- Open-Path Detectors: Utilizing infrared or laser technology, open-path detectors monitor gas concentrations along a continuous line, often spanning dozens or hundreds of meters. They excel in large, open areas like pipelines, perimeters, or storage yards, where gas clouds might disperse beyond the reach of point detectors.
- Diffusion Detectors: These rely on the natural movement of gas molecules into the sensor. Simple and cost-effective, they are effective for monitoring the immediate vicinity but lack the ability to sample air from distant locations.
- Sample-Draw (Pumped) Detectors: Equipped with a pump, these detectors actively draw air samples through tubing from remote or inaccessible areas, making them suitable for complex facilities or confined spaces where gas might accumulate away from the sensor.
The choice of detector type depends on factors such as the size of the area, the nature of the gas, and the layout of the site being monitored.
Applications of Fixed Gas Detectors
Fixed gas detectors are deployed across a wide range of industries and environments, reflecting their versatility and critical role in safety.
- Industrial Settings: In chemical plants, oil refineries, and manufacturing facilities, fixed detectors monitor for flammable or toxic gases that could result from leaks, spills, or process failures. For example, ammonia detectors are vital in refrigeration plants, while hydrogen sulfide detectors are essential in oil and gas extraction.
- Commercial Spaces: In office buildings, parking garages, or boiler rooms, fixed detectors protect occupants by detecting carbon monoxide from vehicle exhausts or natural gas from heating systems, preventing poisoning or explosions.
- Mining and Tunneling: Underground operations rely on fixed detectors to monitor methane and oxygen levels, where gas buildup or depletion can lead to deadly incidents.
- Residential and Public Safety: Though less common, fixed detectors are increasingly used in homes, schools, or hospitals with gas appliances, ensuring early detection of leaks from stoves, heaters, or fuel lines.
In each case, fixed gas detectors serve as a proactive safeguard, offering constant vigilance where human oversight alone would be insufficient.
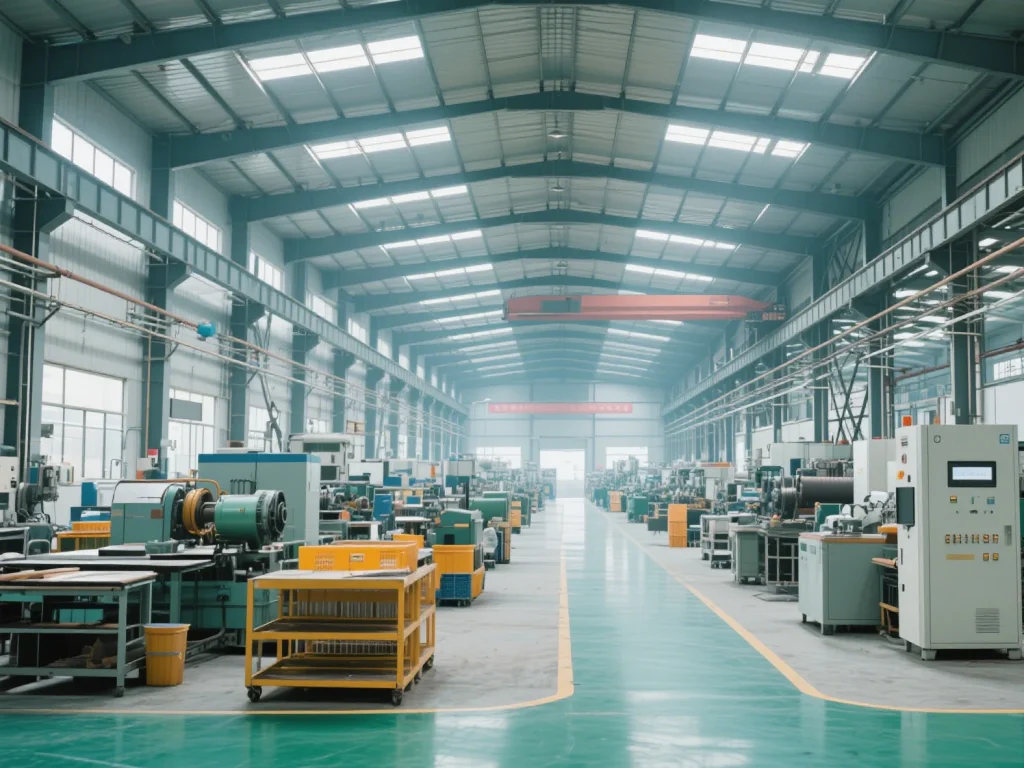
Benefits of Fixed Gas Detectors
The widespread use of fixed gas detectors is driven by several key advantages that enhance safety and operational reliability.
- Continuous Protection: Operating 24/7, fixed detectors provide uninterrupted monitoring, catching leaks that might occur during off-hours or in unattended areas—something portable detectors cannot achieve.
- Early Warning System: By detecting gas at low concentrations, these devices allow for intervention before conditions become hazardous, reducing the likelihood of fires, explosions, or health risks.
- Automation and Integration: Many fixed detectors are linked to automated systems, enabling responses like activating fans, closing valves, or alerting emergency services without human intervention, thus minimizing response time and error.
- Durability: Built for long-term use, fixed detectors are often designed to withstand harsh conditions—extreme temperatures, humidity, or dust—ensuring reliable performance over time.
These benefits make fixed gas detectors a cornerstone of modern safety protocols, particularly in high-risk environments.
Challenges and Considerations
Despite their effectiveness, fixed gas detectors come with challenges that require careful planning and management.
- High Initial Costs: Installing a network of fixed detectors, especially in large facilities, involves significant upfront expenses for equipment, wiring, and integration. This can be a barrier for smaller operations.
- Maintenance Requirements: Sensors must be regularly calibrated and tested to maintain accuracy, which demands trained personnel and can interrupt operations. Some sensors also have a limited lifespan, necessitating periodic replacement.
- Limited Coverage: Fixed detectors only monitor their designated areas, so insufficient placement or poor site design can leave gaps in protection. Comprehensive risk assessments are essential to ensure full coverage.
- Environmental Interference: Dust, moisture, or temperature extremes can affect sensor performance, requiring robust designs or protective enclosures to maintain reliability.
Overcoming these challenges involves selecting detectors suited to the environment, budgeting for maintenance, and strategically planning their deployment.
Conclusion
Fixed gas detectors are indispensable tools in the quest to manage and mitigate the risks posed by hazardous gases. Their ability to provide continuous, reliable monitoring makes them a vital component of safety systems in industries, commercial spaces, and beyond. While they require investment and upkeep, their capacity to prevent disasters—saving lives, protecting assets, and preserving the environment—far outweighs the costs. As technology evolves, fixed gas detectors are becoming smarter, with features like remote monitoring, predictive maintenance, and enhanced sensitivity, further strengthening their role in safety. Whether safeguarding a sprawling refinery or a modest home, these devices stand as silent, steadfast protectors, ensuring that the invisible threats of gas leaks are met with swift and effective action.