In the complex and hazardous environment of shipbuilding, confined spaces pose significant safety risks due to potential gas accumulation, oxygen deficiency, or toxic fume exposure. Fixed gas detectors are indispensable tools for ensuring worker safety, compliance with maritime regulations, and operational efficiency. This article explores the technical requirements, applications, and advancements of fixed gas detection systems in confined spaces within the shipbuilding industry.
Understanding Confined Spaces in Shipbuilding
Confined spaces in shipyards include:
- Cargo holds and ballast tanks
- Engine rooms and boiler rooms
- Pipe systems and ventilation shafts
- Storage compartments for hazardous materials
These areas often contain residual gases (e.g., hydrogen sulfide, methane, carbon monoxide) from welding, painting, or fuel residues. Oxygen levels can drop below safe thresholds (<19.5%) during inert gas blanketing or prolonged sealing. Fixed gas detectors provide continuous monitoring to prevent accidents like explosions, asphyxiation, or chemical poisoning.
Key Technical Requirements for Fixed Gas Detectors
1. Sensor Technology
- Infrared (IR) Sensors: Ideal for detecting hydrocarbons (e.g., methane, propane) with high accuracy and immunity to poisoning.
- Electrochemical Sensors: Detect toxic gases (CO, H₂S) and oxygen levels, offering fast response times.
- Catalytic Combustible Sensors: Monitor flammable gases but may require frequent calibration.
2. Environmental Resilience
- IP Rating: IP67/IP68 protection against water ingress and dust in wet or corrosive environments.
- Corrosion-Resistant Materials: Stainless steel or galvanized carbon steel housings to withstand saltwater spray and chemical exposure.
- Temperature Range: Operation in extreme conditions (-40°C to 70°C) typical of shipbuilding yards.
3. Integration & Alarm Systems
- Modular Design: Expandable systems for large vessels or complex layouts.
- Visual/Audible Alarms: Multi-level alerts (e.g., amber for gas detection, red for emergency).
- Remote Monitoring: Integration with IoT platforms for real-time data analysis and predictive maintenance.
Applications in Shipbuilding Confined Spaces
1. Cargo Hold Safety
During construction, cargo holds may accumulate gases from welding electrodes or paint solvents. Fixed detectors ensure oxygen levels remain above 19.5% and flammable gas concentrations stay below 10% of the Lower Explosive Limit (LEL).
2. Engine Room Monitoring
Leaks from fuel lines or exhaust systems can release CO or NO₂. Detectors trigger ventilation systems or shutdown protocols to prevent fatal exposures.
3. Ballast Tank Inspection
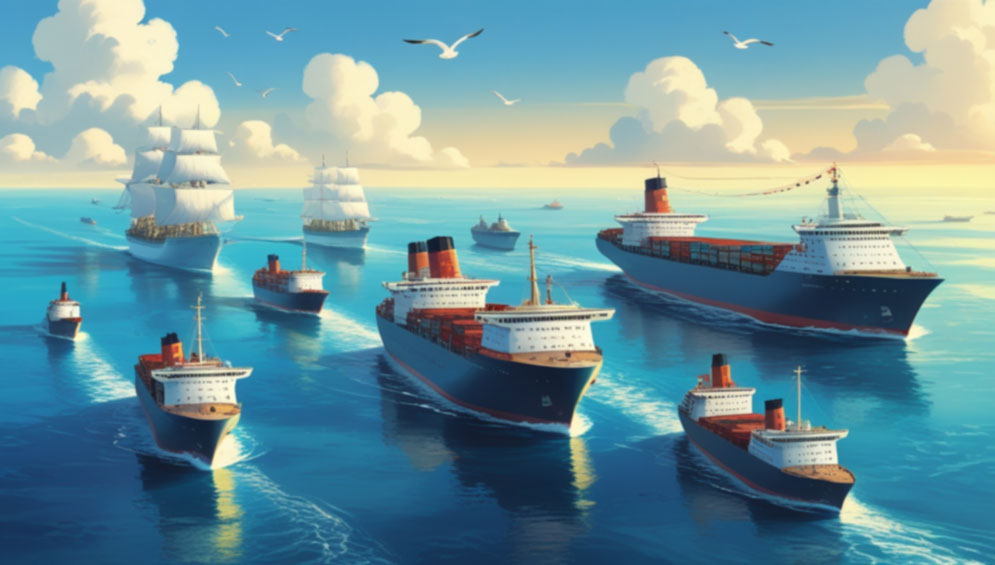
Ballast tanks often contain residual hydrocarbons or hydrogen sulfide from biological activity. Fixed systems alert workers before entry, reducing the risk of sudden gas releases.
4. Pipe System Maintenance
Toxic gases like ammonia (used in refrigeration systems) require continuous monitoring during pipe welding or repair.
Regulatory Compliance and Standards
Shipbuilding must adhere to international regulations:
- IMO SOLAS Chapter II-2: Mandates gas detection systems in engine rooms and cargo areas.
- ISO 13702: Specifies performance requirements for gas detectors in marine environments.
- IEC 60079-29-1: Guidelines for gas detection in explosive atmospheres.
Non-compliance can lead to project delays, fines, or certification denials. Fixed gas detectors help shipyards meet these standards by providing verifiable safety data.
Case Study: Gas Detection in a Cruise Ship Construction
A major shipyard reduced confined space incidents by 60% after installing advanced fixed gas detection systems in a cruise ship project. Key improvements included:
- Multi-Gas Sensors: Simultaneously monitoring O₂, CO, and H₂S in ballast tanks.
- Wireless Networking: Real-time alerts to supervisors via mobile apps.
- Historical Data Analysis: Identified recurring gas sources (e.g., welding torches) for process optimization.
This case demonstrates how proactive monitoring enhances safety and operational efficiency.
Advanced Features for Future-Proofing
- AI-Powered Analytics: Machine learning predicts gas leaks based on historical patterns and environmental factors.
- Low-Power IoT: Batteryless sensors with energy harvesting technology reduce maintenance costs.
- Explosion-Proof Design: ATEX/IECEx certification for use in Zone 0/1 hazardous areas.
- 3D Mapping Integration: Overlay gas concentration data onto BIM models for precise risk assessment.
Choosing the Right Fixed Gas Detection System
When selecting a system, shipyards should consider:
- Certifications: Look for DNV GL, Lloyd’s Register, or USCG approval.
- Calibration Requirements: Automatic self-calibration reduces downtime.
- Scalability: Expandable systems accommodate growing vessel sizes.
- Cost of Ownership: Balance upfront investment with long-term maintenance savings.
Conclusion
Fixed gas detectors are non-negotiable for safety in shipbuilding confined spaces. By combining cutting-edge sensor technology, robust materials, and regulatory compliance, these systems protect workers, prevent accidents, and ensure project timelines. As the industry evolves, integrating AI and IoT will further enhance their effectiveness, solidifying their role as a cornerstone of maritime safety.