In industries where hazardous gases pose significant risks—such as oil and gas, chemical manufacturing, mining, and wastewater treatment—gas detectors are lifelines. These devices monitor ambient gas concentrations, triggering alarms to prevent explosions, fires, or toxic exposures. However, their effectiveness hinges on one critical practice: calibration. This comprehensive guide explores the science, procedures, and best practices of gas detector calibration, emphasizing its role in safeguarding lives and assets.
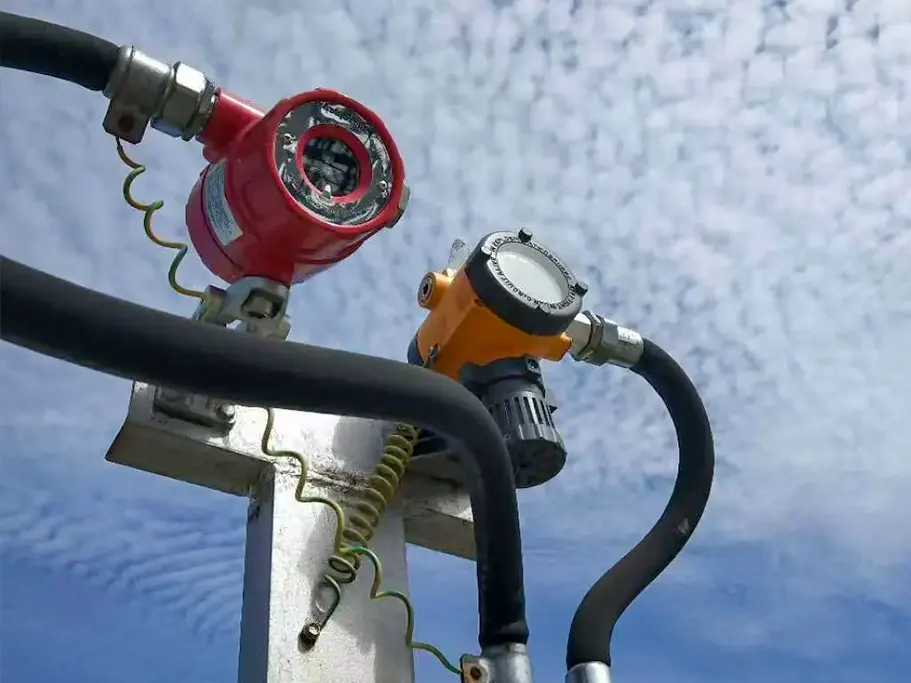
The Critical Importance of Gas Detector Calibration
Gas detectors are only as reliable as their last calibration. Here’s why regular calibration is non-negotiable:
- Safety Compliance:
- Regulatory bodies (e.g., OSHA, ISO 6974, EN 50545) mandate calibration to ensure compliance with workplace safety standards.
- Uncalibrated detectors may fail to alert workers to dangerous gas levels (e.g., methane, CO, H₂S), leading to fatal incidents.
- Accuracy Maintenance:
- Sensors degrade over time due to exposure to gases, humidity, or temperature fluctuations. Calibration restores their accuracy.
- A mis-calibrated detector might report false negatives (no alarm when gas is present) or false positives (unnecessary evacuations).
- Equipment Longevity:
- Routine calibration extends sensor lifespan by identifying and addressing wear early.
- Proper maintenance reduces costly replacements and downtime.
- Legal Liability:
- In the event of an accident, uncalibrated equipment can lead to legal consequences for non-compliance.
Understanding Gas Detector Calibration: Key Principles
Calibration is the process of comparing a detector’s readings to a known reference (standard gas) and adjusting it to ensure accuracy. Key terms include:
- Zero Calibration: Adjusting the detector to read 0% gas in a clean, gas-free environment (e.g., ambient air for combustible gases).
- Span Calibration: Adjusting the detector to read a precise gas concentration (e.g., 50% of the Lower Explosive Limit [LEL] for combustible gases).
- Multi-Point Calibration: Verifying accuracy across a range of concentrations (critical for toxic gas detectors with narrow safe limits).
- Drift: Gradual sensor deviation from true readings, necessitating periodic calibration.
Gas Types and Calibration Requirements
Gas Category | Examples | Calibration Focus | Standards |
---|---|---|---|
Combustible Gases | Methane, LPG | LEL (% of explosion limit) | ISO 6974, EN 50545 |
Toxic Gases | CO, H₂S, NO₂ | ppm (parts per million) | OSHA 1910.146, ANSI/ISA 92.0.01 |
Oxygen (O₂) | Hypoxia/Enrichment | % Vol (20.9% in ambient air) | EN 45544-2 |
Step-by-Step Calibration Procedure
1. Preparation
- Gather Tools:
- Standard gas cylinder (certified concentration, e.g., 50% LEL methane).
- Flow regulator, tubing, and calibration cap.
- Manufacturer’s manual, calibration logbook, and safety equipment (PPE).
- Environment:
- Calibrate in a well-ventilated area away from gas sources.
- Ensure stable temperature (20–25°C) and humidity (40–60% RH).
2. Zero Calibration
- Power on the detector and allow it to stabilize (15–30 minutes).
- Expose the sensor to clean air (e.g., use a zero gas or ambient air verified as gas-free).
- Initiate zero calibration via the detector’s interface or software.
- Confirm reading: 0% for combustible/toxic gases, 20.9% for O₂.
3. Span Calibration
- Introduce the standard gas at the recommended flow rate (e.g., 0.5–1.0 LPM).
- Wait for the reading to stabilize (typically 60–90 seconds).
- Adjust the detector to match the standard gas concentration.
- Verify accuracy: ±5% of the standard for combustible gases, ±2% for toxic gases (per manufacturer specs).
4. Multi-Point Calibration (Optional)
- For toxic gases or critical applications, test intermediate concentrations (e.g., 25%, 75% of the alarm setpoint).
- Ensure linearity across the measurement range.
5. Post-Calibration Checks
- Record results (date, gas type, concentrations, technician name).
- Test alarm setpoints (e.g., low/high alarms for CO: 35 ppm/200 ppm).
- Perform a bump test (expose to a low gas concentration) to validate response.
6. Frequency
- Manufacturer Guidelines: Typically every 3–12 months (e.g., quarterly for H₂S detectors in oil fields).
- Trigger Events: After sensor replacement, physical damage, or exposure to high gas concentrations.
Common Challenges in Gas Detector Calibration
- Sensor Age and Wear:
- Electrochemical sensors (for toxic gases) have a lifespan of 2–3 years; replace before calibration if expired.
- Gas Interference:
- Cross-sensitivity (e.g., H₂S affecting a CO sensor) requires gas-specific calibration.
- Environmental Factors:
- High humidity or temperature extremes can skew readings (use environmental chambers for precision).
- Human Error:
- Incorrect gas flow rates or contaminated calibration equipment lead to faulty results.
Best Practices for Effective Calibration
- Standardization:
- Use NIST-traceable standard gases (e.g., Scott Safety, MSA certified cylinders).
- Follow ISO 17025-accredited procedures for labs.
- Documentation:
- Maintain digital or paper logs with calibration dates, results, and adjustments (critical for audits).
- Training:
- Certify technicians in gas detector operation and calibration (e.g., via IECEx or NEBOSH courses).
- Automation:
- Use smart calibration tools (e.g., MSA ALTAIR Connect, Draeger CalSoft) for remote monitoring and data analytics.
- Preventive Maintenance:
- Clean sensor filters, inspect tubing for leaks, and replace worn components before calibration.
Regulatory Standards and Compliance
Region | Standard | Requirements |
---|---|---|
USA | OSHA 1910.146 (Permit-Required Confined Spaces) | Quarterly calibration for confined space entry |
EU | EN 50545-2 (Gas Detectors) | Annual calibration, documented records |
Australia | AS 4785 (Gas Detectors) | Six-monthly checks for high-risk industries |
Global | ISO 9001 (Quality Management) | Calibration as part of quality system audits |
Case Study: Calibration in the Oil and Gas Industry
A major offshore oil platform in the North Sea implemented a rigorous calibration program:
- Issue: Frequent false alarms and missed H₂S detections due to uncalibrated sensors.
- Solution:
- Quarterly calibration of all detectors (316 units: 304 for toxic gases, 12 for O₂).
- Deployed automated calibration software to track sensor health.
- Result:
- 90% reduction in false alarms.
- Zero H₂S-related incidents over 24 months.
- Compliance with IMO (International Maritime Organization) regulations.
Emerging Trends in Gas Detector Calibration
- IoT and Remote Calibration:
- Wireless detectors (e.g., Honeywell BW™ Solo Connect) enable remote diagnostics and cloud-based calibration logs.
- AI-Powered Predictive Maintenance:
- Machine learning algorithms predict sensor drift before calibration intervals (e.g., Siemens Gas Detectors).
- Green Calibration:
- Eco-friendly standard gases (e.g., recycled methane) reduce environmental impact.
Choosing a Calibration Service Provider
When outsourcing calibration:
- Certifications: ISO 17025, IECEx, or manufacturer (e.g., RKI Instruments authorized service centers).
- Turnaround Time: Critical for industries with tight schedules (e.g., 24-hour rush services).
- Reporting: Detailed certificates with traceability to national standards.
- On-Site Services: Ideal for large installations (e.g., refineries, chemical plants).
Conclusion: Calibration—The Foundation of Gas Safety
Gas detector calibration is not a routine task; it is a strategic investment in safety, compliance, and operational excellence. By adhering to standardized procedures, leveraging advanced tools, and prioritizing training, industries can ensure their detectors perform flawlessly when lives are on the line.
In an era of increasing regulatory scrutiny and technological innovation, calibration remains the cornerstone of gas safety. For professionals in high-risk sectors, the question is not “Should we calibrate?” but “How can we calibrate better?”
Ready to optimize your gas detector calibration program? Partner with certified providers or invest in in-house tools to elevate safety and efficiency. Your next calibration could save a life.